Understanding the Lifespan of Different Commercial Roofing Materials
Learn more about the lifespan of different commercial roofing materials, including EPDM and TPO, as well as factors that influence a roof’s lifespan.
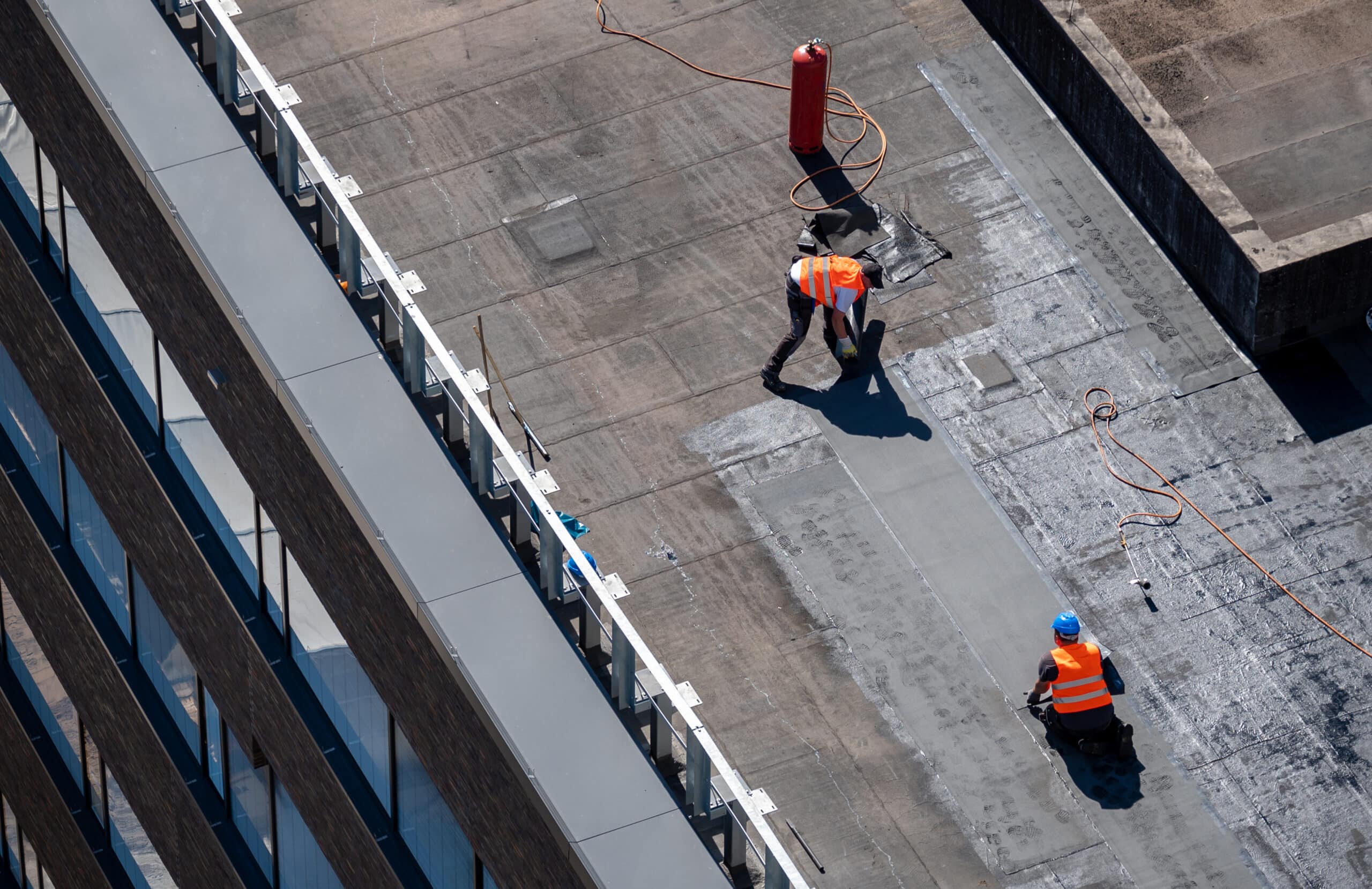
Learn more about the lifespan of different commercial roofing materials, including EPDM and TPO, as well as factors that influence a roof’s lifespan.
The roof is the most important part of a commercial building, protecting the interior of the building from elemental damage. However, most roofing systems only last 20 to 30 years, depending on the material and its maintenance, so property owners are likely to have to replace their roofs at some point.
When it’s time to replace your roof, one of the most significant factors to consider when selecting a system is the type of material it’s made from.
Built-up roofing, or BUR, is a multi-layer system commonly used on flat or low-slope roofs. A BUR system consists of alternating layers of bitumen (better known as asphalt) and reinforcing fabric, creating a durable, waterproof membrane. Layers are alternated with hot tar and stabilized by a layer of smooth stone. Modern BUR systems use more advanced materials like fiberglass membranes instead of traditional tar paper. BUR roofs can last for up to 30 years.
Modified bitumen (MB) is a waterproof roofing material made from a combination of asphalt, rubber, and fiberglass. MB is a more cost-effective alternative to built-up roofing and can last for up to 30 years. These layers include a base sheet, one or more ply sheets, and a cap sheet. Modified bitumen roofs are lighter and easier to install than built-up roofing and offer superior flexibility and thermal resistance. Modified bitumen is also ideal for both flat and low-slope roofs.
Ethylene Propylene diene monomer, or EPDM roofing, is known for its durability, weather resistance, and easy installation on both flat and low-slope roofs. Available in large sheets, this installation reduces the number of seams on the roof. EPDM roofs tend to last 15 to 25 years, but can last for up to 50 years (yes, 50!) if maintained properly.
Thermoplastic polyolefin (TPO) roofing is a single-ply membrane crafted from ethylene-propylene rubber and polypropylene. It’s white and reflective, which helps improve energy efficiency. TPO roofs tend to last for up to 20 years and can be installed on flat and low-slope roofs. However, it’s a relatively new material on the market and has undergone several reformulations, so its lifespan may vary. At this time, its long-term performance isn’t known.
Polyvinyl chloride (PVC) roofing is a single-ply membrane known for its durability, flexibility, weather resistance, and chemical resistance. It can last anywhere from 20 to 30 years and is typically installed on flat and low-slope roofs.
As the name implies, metal roofing is crafted from various types of metal, including aluminum, copper, and zinc. One of the biggest advantages of metal roofing is its long lifespan, around 80 years. The only disadvantage is that metal roofing is not suitable for flat roofs.
Green roofs, or “living roofs,” have a layer of vegetation planted on top of the waterproofing membrane and have many sustainability benefits. While they can be installed on flat and low-slope roofs, they are more commonly found on flat roofs because plants and soil are more stable on flat surfaces, flat roofs allow for better water retention, and they can distribute the load more evenly than low-slope roofs. Green roofs can last for up to 20 years, depending on maintenance.
Beyond the material the roofing system is made from, there are a variety of other factors that influence a roof’s lifespan, including climate/environmental conditions, installation quality, maintenance practices, and material quality.
Fluctuating temperatures can cause roofing materials to expand and contract, which may lead to cracking. High winds and frequent severe weather can also take their toll on a roof by putting additional stress and wear on the materials. High humidity can even lead to mold and mildew growth, which can cause premature material wear. It all underscores the importance of ensuring you install the right type of roof material based on the type of climate your property is in.
Poor workmanship, hands down, is the biggest reason for premature roofing failure. That’s why it’s important to work with qualified professionals like L&S Home Improvements. We ensure quality in our work by only working with manufacturers and products we know and trust, preparing and protecting the building, and offering guarantees after we complete the work.
We also offer silicone coatings, which can be applied over TPO, concrete, steel, aluminum, and membrane roofing. These coatings prevent corrosion, abrasion, and other damage and further extend the lifespan of the property. Furthermore, these fluid applied coating systems offer excellent tax incentives for their owners!
Yearly maintenance is key to flat and low-slope roof longevity. We suggest having your roof inspected annually so small issues can be identified and repaired before they have a chance to become big, expensive, and potentially disruptive. It is common to find clogged roof drains, leaky A/C units, or seam failures. When you choose L&S Home Improvements for your roof installation, we help ensure proper maintenance by enrolling you in our maintenance program.
Choosing the right type of roof material is one thing, but making sure the material is high quality is another. High-quality materials are more durable, require less maintenance, and stand-up better to temperature swings and weather events. You also ensure better quality materials by working with a reliable installation service provider like L&S Home Improvements.
If your commercial property is experiencing any of the above signs, consider scheduling an inspection today.
L&S Home Improvements is a family-owned and operated commercial roofing contractor committed to quality and customer satisfaction. We’re proud to provide installation, repair, and maintenance services to businesses throughout Macomb, Oakland, and Wayne counties. We know how critical a quality roof is to the operation of any business, so we’ve partnered with the best roofing material manufacturers in the industry.
If you’re experiencing roof damage and need help finding the best solution for your business, please contact us today to schedule a free inspection and quote.